为深入贯彻落实党中央、国务院关于碳达峰、碳中和的重要决策部署,完整、准确、全面贯彻新发展理念,坚决遏制“两高”项目盲目发展,践行“宜业尚品、造福人类”建材行业发展目标,科学做好建筑陶瓷行业节能降碳改造升级,推动建筑陶瓷行业节能降碳和绿色转型,根据《关于严格能效约束推动重点领域节能降碳的若干意见》《高耗能行业重点领域节能降碳改造升级实施指南(2022年版)》《工业重点领域能效标杆水平和基准水平(2023年版)》《建材行业碳达峰实施方案》,制定本技术指南。
一、总体要求
完整、准确、全面贯彻新发展理念,科学处理发展和减排、短期和中长期的关系,突出标准引领作用,深挖节能降碳技术改造潜力,按照“因业施策”“因企施策”“一线一策”的原则,加快推进建筑陶瓷行业节能降碳步伐,带动全行业绿色低碳转型,从而推动整体能效水平明显提升,碳排放强度明显下降,确保如期实现碳达峰目标。
二、遵循原则
因地制宜,综合考虑技改投资与收益,不以提产为主要目标,采用适宜的技术方案,降低单位产品碳排放,以最优的技术经济指标运行。对拟建、在建项目,应对照能效标杆水平建设实施,推动能效水平应提尽提,力争全面达到或优于标杆水平。对能效落后于行业基准水平的存量项目,明确改造升级和淘汰时限(一般不超过3年),引导企业有序开展节能降碳技术改造,在规定时限内将能效改造升级到基准水平以上,力争达到或优于能效标杆水平;对于不能按期改造完成的项目进行淘汰。
三、现状分析
建筑陶瓷行业是我国国民经济的重要组成部分,是改善民生、满足人民日益增长的美好生活需要不可或缺的基础制品业。2022年,建筑陶瓷行业规模以上企业超过1000家,全国陶瓷砖产量超过90亿平方米,抛釉砖仍是最大主流,产能占比36%,抛釉砖和中板是近两年扩张幅度最大的产品。截至2022年底,建筑陶瓷行业能效优于标杆水平的产能占比小于10%,能效落后于基准水平的产能占比小于5%。建筑陶瓷行业作为落实建材行业碳达峰的重点行业,节能降碳的压力较大,但通过采用先进的技术和装备,也具有较大的提升改造潜力。
受工业和信息化部委托,中国建筑材料联合会按照代表性强、产品链条完整、碳排放和能耗潜力较大、示范作用明显等原则,选取了3家建筑陶瓷生产典型企业,作为落实建材行业碳达峰实施方案的“试验田”,开展解剖“麻雀”式的调查研究,这3家企业在产品创新能力、品牌实力、产销规模与销售渠道等方面具有较强的实力,在建筑陶瓷行业具有一定的代表性、典型性,为本指南提供了主要的基础数据和节能降碳技术路径支撑。
四、主要目标
到2025年,建筑陶瓷行业能效标杆水平以上产能比例达到30%,能效基准水平以下产能基本清零,行业节能降碳效果显著,绿色低碳发展能力大幅增强。
到2030年,能效标杆水平进一步提高,达到标杆水平企业比例大幅提升,行业整体能效水平和碳排放强度达到国际先进水平,为如期实现碳达峰目标提供有力支撑。
五、建筑陶瓷行业节能降碳技术清单
建筑陶瓷行业碳排放分为直接排放和间接排放,直接排放包括燃料燃烧排放和生产过程(碳酸盐分解)排放两部分;间接排放包括陶瓷生产环节中的电力消耗、以及发电、供热和运输等非生产环节的能耗所折合的二氧化碳排放。建筑陶瓷行业二氧化碳排放主要源于陶瓷生产过程喷雾干燥塔热风炉和窑炉燃料燃烧、原料产生的二氧化碳和电力消耗间接产生的二氧化碳。
目前建筑陶瓷行业的燃料结构以天然气和煤炭为主,天然气占建筑陶瓷生产所消耗能源的47%左右,煤炭占建筑陶瓷生产所消耗能源的37%左右。对照碳排放产生环节和影响因素,节能降碳技术包括低能耗烧成、连续式球磨、干法制粉、燃料类及原料类替代等技术,这些技术目前均较为成熟,分别具有不同的节能降碳潜力,可作为指导建筑陶瓷企业进行碳减排优化改造实施的行动指南。
六、陶瓷行业节能降碳技术路径及预期效果
(一)能效提升技术
1.连续球磨及智能调节技术
技术路径:①原料用连续式球磨机粉碎,磨机采用两段或三段结构,通过粗磨、细磨达到所控制的原料细度。进出料均为连续进行,分为开路和闭路两种生产形式。②通过智能调节控制球磨机内泥浆高度从而减少偏心矩,有效降低运行电流;设定电机频率自动调节区间和运行电流的目标区间,在区间内不调节电机频率,超出运行电流区间一定时间则自动调节运行频率。
预期效果:连续式球磨技术可降低电单耗,综合能耗降低0.05~0.10kgce/㎡。(注:本文所有能耗指标与GB21252中使用的能耗指标一致)
2.高铝球石使用和电机替代技术
技术路径:用高铝球替代中铝球,同时根据待研磨物料的粒度粒级特点,运用破碎统计力学原理指导高铝球配比,使破碎概率最大化,或根据研磨产品中存在的问题,采用大小级配球以强化某些粒级的破碎,完成初装球的精准配比;通过采用变频、永磁直驱系统代替传统异步电机+减速器或皮带传动系统技术,提升电动机功率因数和效率。
预期效果:研磨时间缩短20%,综合能耗降低0.01~0.05kgce/㎡。
3.干法制粉技术
技术路径:原料通过立磨或雷蒙磨粉碎、混合,采用过湿(水加入量约12%)造粒、流化床或其他干燥方式料干燥,经筛分和陈腐后制备成干压成型用粉料,同湿法造粒相比,降低大量蒸发水分(22%~25%)的能耗,实现陶瓷生产高效节能。
预期效果:综合能耗降低0.015~0.020kgce/㎡。
4.集成制粉技术
技术路径:将含水率高的泥浆经压滤脱水获得含水率低的泥饼,再将泥饼破碎成小泥块后,经干燥器利用收集的窑炉低温余热干燥得到小泥粒,然后将小泥粒破碎、造粒、优化、分选后得到水分、粒径符合要求的粉料。
预期效果:制粉环节综合能耗降低0.01~0.02kgce/㎡(利用余热),同时降低污染物排放80%~90%。
5.泥浆保温技术
技术路径:经过球磨后成品泥浆温度约55~65℃,如无保温措施,则会冷却到环境温度。如保证泥浆50℃以上进入喷雾干燥塔,则热交换效率提高,减少所需总体热量。
预期效果:降低喷雾塔热风炉化学燃料消耗,生产每吨陶瓷粉料消耗天然气减少0.5m³,综合能耗降低0.01~0.05kgce/㎡。
6.新型喷雾干燥技术
技术路径:①调整喷雾干燥塔本身性能结构,如挑选合适的规格、整体密闭性控制、热风炉的控制和线性燃烧器的使用;②提高热风的进塔温度、降低热风的出塔温度和出塔热风的循环利用;③控制雾化空气压力和流量以及燃料压力和流量,雾化喷嘴的雾化角、喷射高度、喷枪角度;④将出塔热风循环利用到预热泥浆工序,或交换后再利用。
预期效果:综合能耗降低0.020~0.035kgce/㎡。
7.压机多级变压缸节能技术
技术路径:通过多级变压缸技术,实现主油缸内的油压多级增压压力和多级降压压力的可调,扩大调节区间及级别。解决现有高低压转换的液压机不具有多级可调性的问题,满足实际需求,灵活性高,控制方法简单。
预期效果:砖坯压制阶段综合能耗降低0.005~0.010kgce/㎡。另外,有效减少液压系统的发热,降低油温。延长油液、密封件及阀件的寿命,减少泄漏,降低冷却能耗。
(二)碳减排技术路径
1.新型双层节能窑炉技术
技术路径:使用双层双温窑炉取代单层窑,产量大,兼顾上下层同时生产不同厚度、不同规格的高品质产品。
预期效果:日产量可达2万㎡/天,节省能耗30%,碳排放量每年可减少约5000多吨,综合能耗降低0.02~0.03kgce/㎡。
2.低能耗快烧技术
技术路径:通过调整坯料控制细度、选用高钾助熔剂等工艺技术,通过调整窑炉低、中、高温区的温度控制,跟踪产品砖形、辊棒痕、体密度、二次变形、断裂模数、综合能耗等相关参数,确定低温快烧的烧成曲线。
预期效果:通过采用低能耗快烧技术,将现有建筑陶瓷产品的烧成温度降低约为100℃,达到1100℃左右烧成,综合能耗降低0.05~0.10kgce/㎡,碳排放减少5%~10%。
3.窑炉余热利用技术
技术路径:通过开发内置式自循环干燥技术和接力回收窑炉冷却余热系统,实现余热高效回收和循环利用,提高热利用效率;优化多层干燥窑和宽体辊道窑的耐火保温结构,集成创新窑砌体和密封结构,提高保温效果,降低窑炉散热。
预期效果:实现窑炉冷却余热和内部热气的高效回收、快速均化、自动控温及循环利用,提高热量的利用效率。预计综合能耗降低0.30~0.40kgce/㎡。
4.窑炉节能技术
①燃烧系统和保温技术
技术路径:通过燃烧技术研究,改进喷枪的使用方式,在窑炉中高温区域进行纳米材料喷涂和窑炉保温材料,以及干燥段窑炉烟气的利用等措施,达到窑炉节能的目的。
预期效果:天然气单耗降低0.15~0.20kgce/㎡。
②高效轻质保温耐火材料应用
技术路径:采用高效轻质保温耐火材料——纳米绝热保温材料、轻质陶瓷纤维代替重质耐火砖,陶瓷窑墙结构将发生革命性的变化。
预期效果:轻质保温耐火材料重量只有重质材料的1/6、容重为传统耐火砖的1/25、蓄热量仅为砖砌式炉衬的1/30~1/10、窑外壁温度可降到30℃~60℃;综合能耗降低0.05~0.10kgce/㎡。
③窑炉空窑自动升降温系统
技术路径:通过智能监控系统,自动判断空窑、稀窑,实现预热段空窑自动降温,缓冷段空窑温度维持,空窑后进砖自动升温功能,减少空窑时不必要的热量损失,减少燃料消耗,从而达到节能降耗的目的。
预期效果:综合能耗降低0.01~0.02kgce/㎡,碳排放减少3%~5%。
④窑炉SRS烟气换热系统
技术路径:利用先进的自清洁的板式换热器,将烟气换热成干净的热空气,可用于窑前干燥器、釉线干燥器、前助燃风机,减少干燥器腐蚀和落脏。提高窑炉余热利用,从而降低能耗。
预期效果:综合能耗降低0.05~0.10kgce/㎡,碳排放减少10%~15%。
5.近净尺寸成型技术
技术路径:通过设计适用于工业化生产的粉料均化设备及粉料降温装置,同时结合精密的布料系统及辊压成型技术,改善了粉料颗粒级配,提高了粉料均匀度;创新设计了一种有利于烧成温度和能耗控制的新型节能燃烧器,根据制品烧成特点精细化调节燃气与助燃气比例,对稳定窑内温度、缩小窑炉断面温差具有显著效果。
预期效果:系统解决瓷质砖生产尺寸偏差大、磨边废料多、资源消耗高的行业共性难题。行业综合能耗降低0.10~0.15kgce/㎡。
6.连续辊压成型技术
技术路径:采用双钢带连续辊压成型设备,将均匀布在钢带上的粉末层通过上下设置的一对主压辊,连续辊压成陶瓷砖坯。相对于传统的模压成型陶瓷砖自动液压机,辊压机的装机功率低、液压油消耗很少、设备结构简单重量轻、成型速度快、可连续压制成型,可大幅降低瓷砖生产砖坯压制成型阶段的能耗。
预期效益:每平方米瓷砖成型单耗降低0.01~0.02kgce/㎡。
7.构建智能化能源管理体系
技术路径:构建智能化能源管理体系,对重点设备进行能耗动态监测,建立和完善能效测评、用能标准、能耗统计、能源审计、能效公示、用能定额、节能服务等各项能源运行管理指标,找出能源浪费环节,做好管控及统计,精准定位能源浪费点,从而降低运营能耗。
预期效果:实现生产线定员定岗减少20%,预计综合能耗降低0.40~0.45kgce/㎡以上,实现全行业减碳20%以上。
8.实施企业智能管控系统
技术路径:以能源和物料为主线,贯穿整个生产,通过互联网等新技术,与生产中所有重点能耗设备信息互通,可实现能源管理、绩效分析、生产调度、设备运行维护、故障分析、设备监控、系统优化运行等全面功能。
预期效果:实现车间员工减少80%,预计综合能耗降低0.10~0.15kgce/㎡以上,实现产能提高10%。
(三)原料降碳技术
1.污泥替代陶瓷原料技术
技术路径:将污泥作为主要生产原料,掺量可达60%~80%,开发适用于污泥原料配方的干法制粉、干压成型的新生产工艺;采用新工艺可减少球磨机、喷雾干燥塔等大功率能耗设备的投入和使用,固废资源化利用不仅大大降低了生产成本,同时也起到了节能降碳的作用。
预期效果:降低原料成本,降低天然气能耗,综合能耗降低0.02~0.03kgce/㎡。
2.建筑陶瓷产品薄型技术
技术路径:采用优化原料配方体系、坯体增强、增韧技术以及增大成型压力、调整烧成制度等方式,降低建筑陶瓷砖的坯体厚度。
预期效果:陶瓷砖由目前普遍生产厚度降低20%(从10mm降到8mm),则每年至少节约能源500万吨标准煤,少用原料2000万吨以上,减少CO2排放量约1300万吨,同时综合能耗降低0.05~0.10kgce/㎡。
3.建筑陶瓷产品轻质技术
技术路径:采用陶瓷生产废料为主要原料,通过加入特殊发泡材料,在高温下烧制成一种具有陶瓷性能、比重小的新型装饰材料。
预期效果:轻质新型建材与同类产品相比,单位面积建筑陶瓷材料用量降低50%以上,节约60%以上的原料资源,同时综合能耗降低0.03~0.05kgce/㎡。
(四)燃料、能源替代技术
1.清洁能源利用技术
技术路径:以天然气代替煤转气。天然气的单位热值含碳量为15.3(tC/TJ),碳氧化率为99%,煤转气的含碳量为27.8(tC/TJ),碳氧化率为94%;在发热量相同情况下用天然气燃烧时产生的碳排放可比标准煤低近40%。预期效果:采用天然气代替煤炭,可减排二氧化碳接近40%,综合能耗降低0.4~0.5kgce/㎡。
2.生物质能源利用技术
技术路径:采用秸秆、木屑等农林废弃物作为原材料,通过粉碎、烘干、混合、挤压或压块成型等工艺,制备成颗粒状、棒状、块状的新型清洁燃料,配套生物质专用锅炉及辅机设备,采用水冷壁、分段空气、二次风等技术措施,解决生物质燃料燃烧灰分高、易结焦等难题,实现生物质成型燃料替代传统化石能源在窑炉上的成功应用。
预期效果:综合能耗降低0.7~0.8kgce/㎡,按照节约1kgce,减少2.493kgCO2排放计算,每平方米陶瓷砖减少1.75~1.99kgCO2。
3.太阳能利用技术
技术路径:通过在屋顶或其他空闲区域加装太阳能光伏发电系统,满足建筑陶瓷行业生产过程中的部分或全部电消耗。
预期效果:综合电能耗降低0.3~0.4kgce/㎡。
七、不同能耗水平建筑陶瓷企业技术改造提升建议
本指南仅以试点企业提出碳减排技术方案,不同原燃料条件的建筑陶瓷企业根据其实际使用的工艺、设备进行个性化的选择,以达到最大化的节能降碳为目标。各建筑陶瓷企业在实际实施中宜查漏补缺,补短板增强项,最终实现建筑陶瓷综合能耗及碳排放的降低。
本指南以国家发展改革委员会发布的《工业重点领域能效标杆水平和基准水平(2023版)》中定义的基准水平值和标杆水平值为碳减排技术应用目标,为不同能耗水平的建筑陶瓷企业提供对应的碳减排技术应用方案。指南中所列举的碳减排技术方案仅为建议方案,建筑陶瓷企业在实际应用中可根据具体情况选择使用。
(一)能耗基准水平以下企业节能降碳技术改造建议
综合能耗基准水平以下的企业往往是采用较落后的设备和工艺,通过设备升级或工艺优化可以降低建筑陶瓷生产综合能耗,使其综合能耗达到基准水平或标杆水平。
为达到综合能耗基准水平需要将建筑陶瓷生产的设备及工艺提升至目前主流的连续球磨及智能调节技术、高铝球石使用和电机替代技术、干法制粉技术、泥浆保温技术、低能耗快烧技术、窑炉余热利用技术、连续辊压成型技术、污泥替代陶瓷原料技术等。
(二)能耗标杆水平以下企业节能降碳技术改造建议
综合能耗达到基准水平但未达到标杆水平的建筑陶瓷企业基本已经采用了先进的设备或工艺,要达到标杆水平需要进一步选择压机多级变压缸节能技术、新型双层节能窑炉技术、建筑陶瓷产品薄型技术和轻质技术等组合降低能耗。
采用构建智能化能源管理体系、实施企业智能管控系统、生物质能源利用技术和太阳能利用技术中的一项或多项可大幅降低能耗水平及CO2的排放量,使不同能耗水平的建筑陶瓷企业直接达到标杆值水平。
八、未来建筑陶瓷企业碳减排技术展望
提出未来需要研发攻关的具有前沿性、颠覆性,具有流程再造的绿色低碳技术。
(一)新能源技术
开发适用于氢能、氨能等其他清洁能源的系统燃烧技术与装备,以替代传统的化石燃料;探讨电烧辊道窑技术的应用,以提高能效和降低碳排放。
(二)推广原料标准化、集约化发展
鼓励公司内部优先实现原料标准化,逐步形成原料、粉料的成品化,进一步对原料集中均化处理,建立原料标准化生产基地,建立陶瓷原料标准体系。
(三)制粉工艺的突破
推广干法制粉技术、干法与湿法造粒粉结合技术,研发泥浆高效电解质,以提高原料利用率和质量,减少水分和污染物的排放。
(四)新型解胶剂以及坯体增强剂的开发
研发新型解胶增强剂,同时具有坯体增强作用和解胶作用,减少减水剂类添加剂的加入量,综合降低生产制造成本及节能降碳效果。
(五)低碳窑炉及喷塔研发
探求更新低碳窑炉及喷塔设备的研发,加快突破建材窑炉碳捕捉、利用与封存技术,提高窑炉及喷塔装备水平。
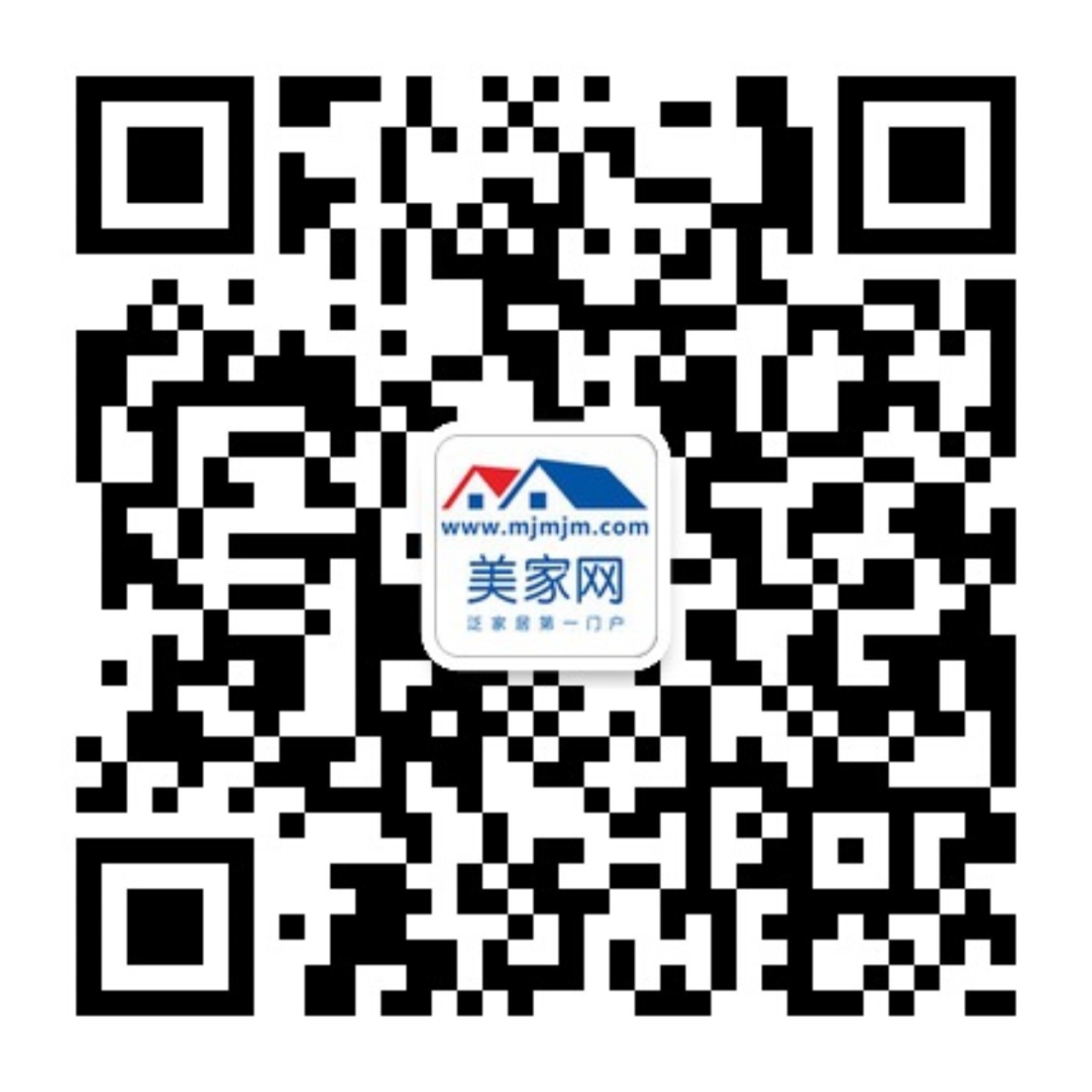